There are many types of welding and welding machines. Among them, stick welding is probably the most hardcore process there is. But if you’re not a pro, there’s a long road ahead of you before you can start learning about stick welding.
MIG, TIG, and arc welding are the bread and butter of most professionals and hobbyists. You may think that they’re always interchangeable, but they’re not. Here are some of the key differences that you need to learn before you pick up a welder and go to town with it.
Why It’s Important to Understand the Differences
You may think that MIG, TIG, and arc welding are all there is to it, that it’s enough to understand three terms and be all set to buy and use a welder on your own. Sadly, that’s not the case. Once you start reading a bit about welders, you quickly learn that there are way too many specialty terms used to describe different processes and welding machines.
For example, you see the term MIG welding thrown around a lot, right? Did you know that it’s actually GMAW welding and that the acronym stands for Gas Metal Arc Welding? Though commonly referred to as MIG, most professionals, as well as some manufacturers, may not use the MIG designation on their welders.
It’s stuff like that that can confuse beginners. Therefore, the purpose of this article is to make the basic terms clearer and easier to grasp.
MIG/GMAW Welding
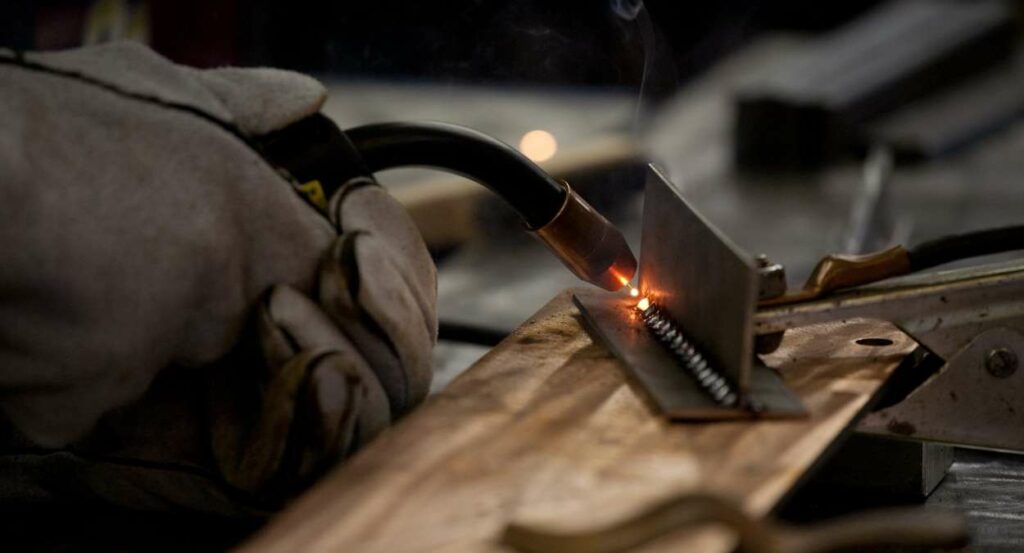
A MIG welder can be a very versatile tool. It can be used on thin and thick sheets of metal, alike. You can use it on sculptures due to the amount of control you can exercise by using the stop trigger. It also doesn’t take a lot of experience to use an MIG welder, compared to other welding machines.
But, how does it really work? MIG welding is achieved by feeding a line through a specially designed gun. By continuously feeding the line of electrodes, an arc will form when the line comes in contact with the metal. This causes the metals to melt together.
In order to ensure a safe and clean weld, a protective gas bubble is created around the weld. Also, the materials don’t fuse together. This is one of the reasons why MIG welding is so versatile, because it allows you to weld multiple types of metals together.
The line of electrodes is a consumable, as is the gas. This means that you constantly have to check your inventory before starting a new project.
TIG/Heliarc/GTAW Welding

GTAW stands for Gas Tungsten Arc Welding. This means that a tungsten electrode is used instead of a consumable line of electrodes. When the tungsten tip heats up the welded material, it will create a weld puddle.
So, there are two big differences between TIG and MIG welding. TIG welding doesn’t use a consumable line on a continuous feed. And, the weld doesn’t contain particles from two different metals. Only the metal that you’re welding creates the weld.
Of course, filler material can be used and is, in fact, recommended if you want to broaden your range of accessible materials. Just know that it’s not necessary.
In terms of uses, TIG welding is a bit more limited. Not by materials, but by the thickness range of the materials that you can use. On the other hand, TIG welding can be easily used on thin, precise, and finesse welds.
Considered by many as the artists’ choice, TIG welding can produce perhaps the most aesthetically pleasing welds. But, it comes with a steep learning curve. Even though you may need to work on thin materials and do light finishing work, you may still want to use MIG welding for steel and aluminum.
Arc/Flux-Cored Welding

Arc welding is often confused for MIG welding. That’s because the said methods use a somewhat similar process. Arc welding also employs a consumable wire on a continuous feed. Unfortunately, this is pretty much the only major similarity.
So, what’s the first difference? The wire used in arc welding features a flux core. This can create a gas shield around the weld, meaning that you won’t need an external gas source to create the shield.
In some designs, often dubbed dual-shielded welding machines, you can also have an external gas supply that creates its own shield. You can use one of those arc welders to produce an even more secure weld. You won’t be able to use it just to have a backup shield generator, if you will.
There are some clear advantages to arc welding. The most important one is, perhaps, the extra mobility you get by not having to drag a large, heavy gas tank around.
Another prominent characteristic of arc welding is welding with minimum wire waste. Because of this, you can use it in heavy-duty applications, such as heavy steel construction projects or for repairing heavy machinery. In fact, an arc welder will be too powerful for thin sheet metal, car maintenance, and other tasks of this nature.
However, aesthetically pleasing welds are not synonymous with arc welding.
What’s the Best Type of Welding?
There’s really no such thing as a universal welder, even though some welding processes can handle a wider range of materials than others. Keep in mind that product waste and generated heat are the key factors in determining what projects you can take on.
Beginners should start with MIG and TIG welding, preferably MIG. They should refrain from using TIG and arc welding, because of the steep learning curve. What about possible applications?
MIG welding can be used for just about anything up to, and including, heavy duty industrial work. TIG welding is the go-to method for finesse work. Arc welding is the ultimate choice for the really heavy stuff on construction sites and large machinery maintenance tasks.
Final Thoughts
Maybe you’re reading this article to prepare yourself for a career in welding. But, most likely, you want to know what welder to use for some basic car and home repair work, maybe even some fancy artwork.
Whichever the case may be, know that welding is a craft which is somewhat easy to pick up but very hard to master. That means that it will take some time before you can comfortably weld without messing up the structural integrity of the connections.